ACTUATION AND MECHANISMS
OVERVIEW
Moog has produced spacecraft motion control products for more than 50 years, dating back to the historic Apollo and Pioneer programs. Today, we offer rotary, linear, and specialized mechanisms for spacecraft motion control needs. Moog is a world-class manufacturer of solar array drives, propulsion positioning gimbals, antenna positioner mechanisms, docking and release mechanisms, and specialty payload positioners.
ANTENNA POINTING MECHANISMS
The wide variety of antenna positioner assemblies are compact, two-axis gimbals which are ideal for supporting and positioning small, medium, and large-sized spacecraft communications antennas. Gimbals can be configured with either elevation over azimuth (shown right) or X-Z (crossed axes, shown below). Several approaches to electrical cable management ranging from cable drums, twist capsules and slip ring assemblies are available.
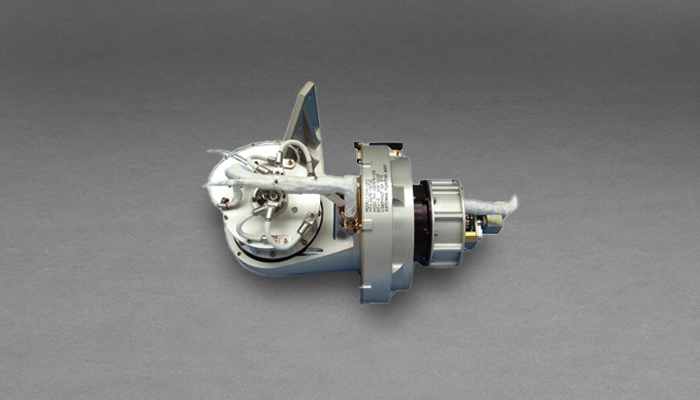
LINEAR ACTUATORS
Moog Linear Actuators use a ball screw or leadscrew to translate the rotary motion of a brushless DC or a stepper motor to linear output motion. The torque transmitted to the output stage is amplified through a gear transmission. The driving motor is a 3-phase, multi-pole, permanent magnet, brushless DC, or stepper motor design. Position is monitored through a linear potentiometer integrated into each unit.
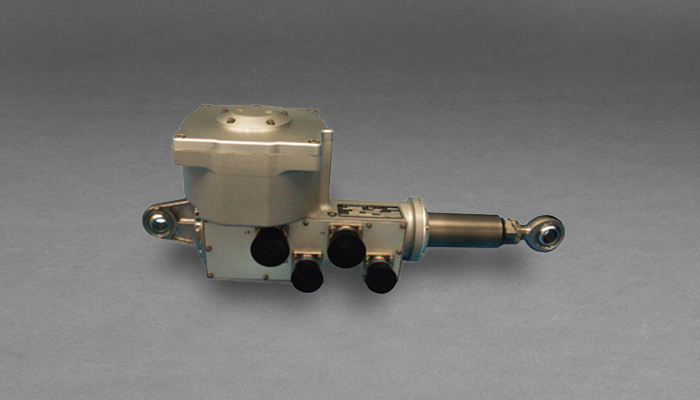
ROTARY ACTUATORS
The Rotary Actuator consists of a small-angle permanent magnet stepper motor coupled with a Harmonic Drive Speed reducer, with a large rotating output flange member. The family of Rotary Actuators is based on heritage design with a wide range of step sizes available.
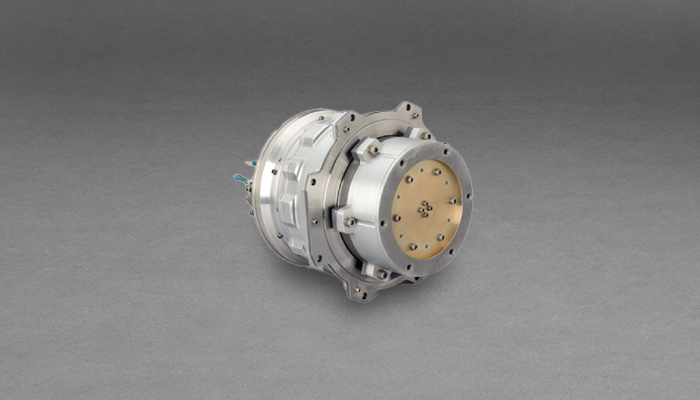
SOLAR ARRAY DRIVE ASSEMBLIES
There are a variety of solar array drive assembly (SADA) options, for both earth orbit and planetary missions. Some options include Single or dual axis, stepper or Brushless DC, Slip Ring, Twist Capsule or Cable Management, and Resolver, Potentiometer or Feedback options.
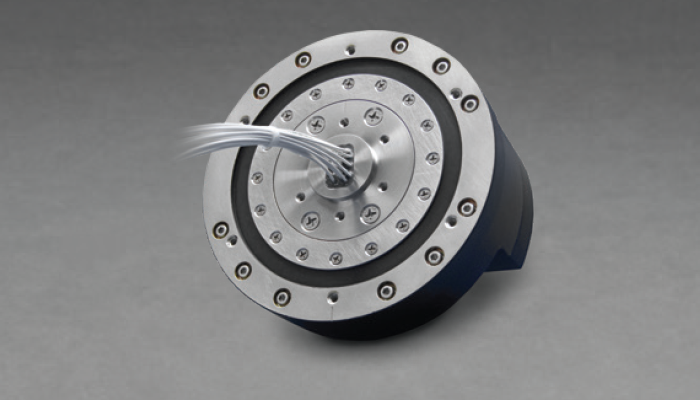
OPTICAL FILTER WHEEL ASSEMBLIES
Moog’s design of Filter Wheel Assemblies is unique in concept and has been used successfully on several space missions. The design is based on integrating the motor rotor with the optical disk thus providing an optimized solution with high torque in the most compact volume and with lower mass. The more conventional design of filter wheels driven by external motors has the design limitation of only two optical disks in a FWA with two motors on opposite sides. The Moog design is not limited by the number of optical disks, as each optical disk is the motor rotor driven by its own stator assembly.
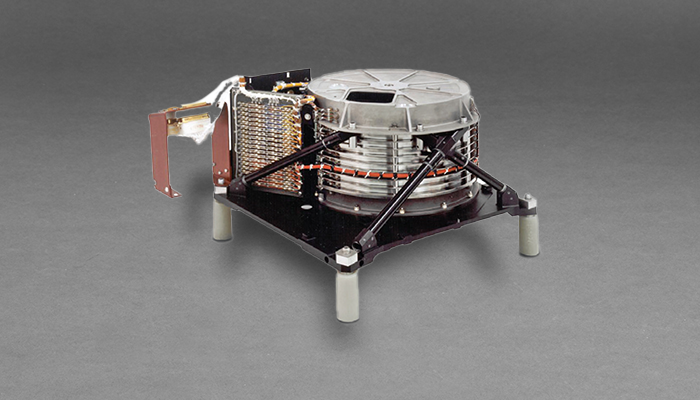
GIMBALS
Moog biaxial gimbals are well suited for performing spaceflight tracking, scanning, and positioning functions. Applications include solar array drives, antenna positioners, and optical telescope and instrument drives.
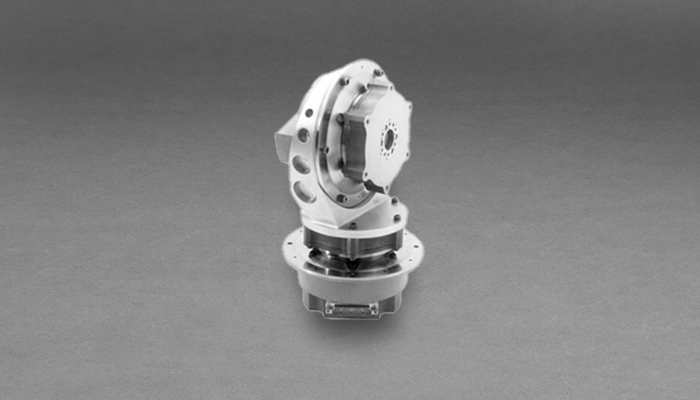