Today’s gas and steam turbine manufacturers continually seek any performance edge they can find. So when one German manufacturer needed a better way to maximize productivity and minimize costly downtime, Moog engineers knew they could help. Tapping into its extensive experience in electric actuation, the Moog team designed and introduced a unique integrated package that was tailored to the customer’s specialized technical requirements — and offered an array of technological advantages as well.
Section view on a typical gas turbine with highlights of the Moog actuators
Advantages of Electric Servo Drive Technology for Turbine Motion Control
Some features of the integrated solution included updating to state-of-the-art technology that offered the customer many advantages over conventional hydraulic designs:
- The usage of a digital controller with integrated fieldbus and self diagnostics was able to provide a much more reliable solution than previously achieved
- A warning device that alerts an operator prior to a malfunction was implemented that helped reduce downtime due to the control of positioning errors, current limits, and environmental influences (e.g., temperature)
- The automatic programming feature of the Moog Motion Controller made maintenance easier, because all changes in parameters (e.g., change of a drive) can be easily handled
- Eliminating hydraulics greatly reduced infrastructure, energy and operating costs, thereby reducing the overall total cost of ownership. For example, in standby mode the energy consumption of an electric system is nearly zero, saving energy costs over hydraulic in an industry with 24/7 operation
With a servo motor that meets requirements for global certifications for hazardous environments, Moog had the core technology and experience in-house to design specialized electric actuators. Combining this core product with our mechanical design capabilities, Moog was uniquely able to address a wide variety of customer demands of turbine control applications.
The Solution
In 2003, Moog designed for this customer a prototype solution for the control of an inlet guide vane of small gas turbines (5-12 MW). The first offering included a several Moog core building block products including a brushless servo motor, a linear servo actuator and a servo drive. It was tested on a Moog test rig as well as in a first application in the field. To this day no reliability issues have been reported and this first approach is still running effectively.
Founded on this successful experience, a long-term beneficial relationship both for the customer and Moog was established. Today Moog is able to deliver electric actuators for various turbine functions, in total up to five electric axes within one gas turbine. Each system is designed and certified with respect to the current directives for operation in an explosive environment.
Scope of Supply
- Software and application know how
- Modular Multi-axis Programmable Motion Controller (MSD)
- Modular Multi-axis Programmable Motion Controller Servo Drive (MSD)
- Explosion-Proof Dynamic Brushless Servo Motor (ExD Series)
- Customized mechanical adaptation of the design
- Procurement of purchased parts, such as operating valves, to customer’s specifications.
- Support including endurance testing, commissioning, field-testing, maintenance and troubleshooting
The Three Electric Axes in Detail
The Moog Fuel Metering System is used to meter air to a gas turbine and it provides some new benefits not available in the conventional design such as improved fault warning and remote monitoring for easier maintenance and diagnostic capabilities. The actuator is used to add air to the exhaust system of the turbine, to achieve better emission values. A highly dynamic servomotor, boosted by a gearbox, is used as the actuation for the system. The servo motor technology used, in conjunction with a rigid clamp coupling, achieves high levels of positioning and repeatable accuracy. An additional customer requirement was to prevent the valve from being closed completely. This is achieved by introducing an internal mechanical endstop.
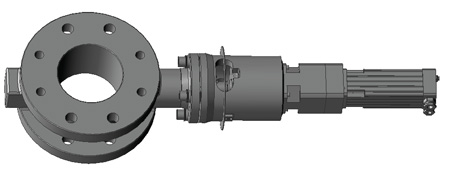
Air Ratio Control Valve
The Moog Fuel Gas Actuator is used to control a linear-actuated fuel gas valve to define the exact flow of fuel gas into the turbine. A highly dynamic servo-motor is used to close the position loop of the adapted valve. The rotation of the motor is converted in conjunction with a precision ball-and-screw spindle actuator into a linear stroke motion. High levels of positioning and repeatable accuracy are achieved. As an additional safety feature the end-stops of the valve can be detected via two proximity switches.
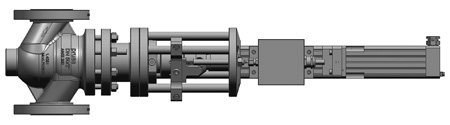
Fuel Gas Actuator
The Moog Inlet Guide Vane Actuator is used to control the position of an inlet guide vane of a gas turbine. This is one of the most important functionalities of the gas turbine control elements, though the revolutions of the turbine are controlled with this actuator by turning the vanes in/out of the gas flow. The rotatable motion of a servomotor is converted into a linear motion by means of a ball screw.

Inlet Guide Vane (IGV) Actuator
Motion Control and Performance
One Moog Motion Controller controls up to five actuators for each turbine. The number of actuators used per machine is detected automatically. Communication to the superior PLC is realized by ProfibusDP and from the motion controller to the actuators via the integrated CANopen profile. In case of an actuator failure, no additional software is needed for parametrization as this realized with the built-in functionality of the MSC Servo Controller. The change of an actuator is detected automatically.
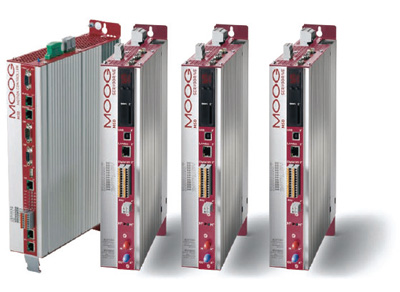
Moog MSD Motion Controller and MSD Servo Drive
The commissioning is typically completed by the service department of the machine manufacturer without any support from Moog. The built-in commissioning interface is used to start up a new turbine.
Conclusion
The project involved electrical, mechanical and software engineers from the Moog facility in Böblingen, Germany working closely together with our customer to realize an innovative solution that met all requirements. The collaboration of a highly motivated project team ensured that Moog was able to deliver the high performance solution required for this challenging application. We are looking forward to further challenges in the power generation market.
Authors
Fabian Erbe is the Engineering Manager Services Europe and he has been with Moog since 2000. He started as an application engineer in the systems group in Böblingen, Germany and worked as an Engineering Team Leader before assuming his new role in the Control Solutions organization. He studied Mechanical Engineering focusing on hydraulics at the Rheinsch Westfälische Technische Hochschule in Aachen, Germany.
Benjamin Wehle is a Design Engineer for Applications of Electromechanical Systems based in Böblingen Germany. He has worked with Moog for two and a half years and studied Mechanical Engineering at the University of Applied Sciences in Pforzheim , Germany.