Moog Hydraulic Simulation Table in CTI Suzhou, China
Today, the pressure on automotive designers has never been more intense. Tighter operating budgets, shorter time to market and fewer resources in the test lab mean test and design professionals must think differently to meet their evolving challenges. What worked just five years ago, in fact, may already be obsolete and ineffective. So where do automotive engineers turn when the stakes are so high on completing their latest design projects?
In test labs around the world, automotive suppliers are turning to simulation tables to bring automotive parts to market faster. Multi-axis testing with a simulation table enables companies to shorten the time required for product testing and quality assurance. These tables can run continuously for several days, a period equivalent to hundreds of thousands of road kilometers. With realistic simulation testing and technology advances, the timeframe to bring a new automotive component to market has been reduced from three to four years to just 18 to 24 months over the last 20 years. Today’s simulation tables are far more accurate and efficient, as well as safer and less expensive, than testing on traditional proving grounds.
As a technology-neutral supplier of test systems, Moog’s engineers work with customers to provide hydraulic and electric technologies and customize key parameters for a simulation table to meet the exact requirements of the test operation. In the past few years, test labs have been increasingly interested in electric actuation systems for mechanical testing. This increase is the result of factors including the advanced capabilities of electric technology and the willingness of test labs to consider new technology to boost their competitiveness. While hydraulic actuation remains the logical choice for most structural test applications, advantages of electric actuation create suitability for many specific test applications.
This article explores four case studies where automotive suppliers are successfully using simulation tables. It provides insights on how these companies selected the right technology (hydraulic or electric simulation tables) and customized its operation to meet unique technical requirements and business objectives.
Hydraulic Test Tables Take Laps for CTI
The Suzhou, China-based Centre Testing International Corporation (CTI), a provider of vehicle components durability testing services, recently selected Moog to provide a customized Hydraulic Simulation Table (H-ST) to test powertrain mount durability (See Fig. 1). CTI wanted the multi-axle road simulation testing capabilities for its customer GM PATAC – a joint venture between General Motors and Shanghai Auto Group.
The H-ST consists of a compact and light platform and base plates on which stress resistant hydrostatic jacks are assembled with rods jutting from the jacks connected to the platform structure. To meet the unique needs of the application, Moog engineers customized the system in several unique ways. Moog designed one rotary actuator with a connection fixture that was used to add torque input to the engine to simulate engine torque output and add force on the test mounts at acceleration/deceleration events. An additional electric heating system was also used to simulate the circumstance temperature of each mount area. Closed loop control of temperature was achieved through a heating gun, PLC controller and temperature sensors, and the temperature set point was determined based on thermal CAE analysis of actual road test data.
To complete its tests on the new system, CTI prepared a vehicle half body, and powertrain assembly and pillars as fixtures for connecting test mounts (engine, transmission, rear end) with the H-ST.
“We were looking for a solution to a particularly complex durability test,” said Lilac Lai, key account manager, CTI Suzhou. “Moog allowed us to comprehensively communicate our goals for the project, translate this vision into a customized solution that met our needs, and deliver on our commitments to our customer.”
Tenneco China’s Challenge
Tenneco China had a long-standing relationship with Moog. When Tenneco China asked Wuxi XinDeBao, an OEM supplier of exhaust pipe sub-systems for major car brands such as Volkswagen, GM, Ford JV, FAW and SAIC, to establish a China-based solution for durability and validation tests, Tenneco knew the motion-control experts at Moog could help XinDeBao with a solution.
As Moog began working with XinDeBao and Tenneco, the motion-control test team in China determined that only a new version of Moog’s Hydraulic Simulation Table 100 kg (H-ST-100) could accurately meet XinDeBao’s requirements for the testing of automobile exhaust pipes. With the Moog H-ST-100 test solution (See Fig. 2), XinDeBao could conduct flex coupling component durability tests to simulate the relevant movements of two boundaries (engine manifold end and exhaust pipe end) in 6 DOF from a real-time time history domain. Time history files are simulated through the Moog Test Controller (H-ST) and Replication and Runner application software, to accurately replicate any specific road conditions needed for the tests. The test system is very compact and provides excellent accessibility during testing.
Moog delivered the new system on schedule and XinDeBao used the H-ST-100 to conduct a successful flex coupling durability test program specifically designed by Moog to handle smaller payloads of up to 100 kg (See Fig. 3). The table is also capable of performing durability evaluations of other small vehicle components.
Jimin Wang, general manager of XinDeBao, said, “Moog’s solution capabilities impressed us, especially compared to the other alternatives considered, which were often oversized, overdesigned, and overpriced for our requirements.”
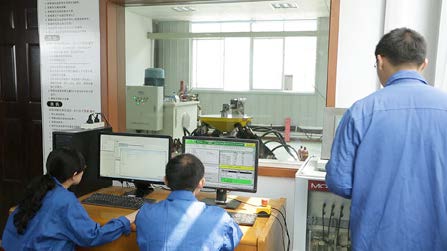
Fig. 3. New Moog Hydraulic Simulation Table with a XinDeBao Metal Hose
being tested in Wuxi XinDeBao, China
Thinking Inside the Tank
When most people think of their vehicle’s fuel tank, it’s a simple thought about keeping it from running dry. For engineers, designing an automotive fuel tank is a complicated (and sometimes costly) challenge. Early in the design phase, engineers must test the pumps for drawing fuel from the tank. Level meters assess the amount of fuel in the tank, and valves make sure air is entering the tank. Introduce velocity, speed and temperature, and designing the tank becomes a not-so-simple endeavor.
Plus, there’s often limited time to do this work, especially when an automobile manufacturer is trying to introduce a new model to the market. Automakers have largely relied on test tracks to design fuel tanks. But taking a vehicle to a certified test track requires a prototype.
When Fiat determined that it was spending too much money taking prototypes to the test track, the company sought a more innovative approach to road testing. The company turned to Moog for an 8 Degrees of Freedom (DOF) simulation table design that would save them both time and money. By using a universal joint to connect a 6 DOF electromechanical simulation table to a 2 DOF tilt table on top for increased pitch and roll motion (See Fig. 4), Moog reproduced higher frequency road profiles, where the tilt table simulates the cornering and acceleration behavior of the vehicle. The 8 DOF test systems enables Fiat to include different conditions during driving that lead to extreme fuel-sloshing effects, such as mountain driving, instant braking or very sharp cornering maneuvers. Software linked to the system replicates time history drive files that were recorded at the test track or perform resonant-frequency research.
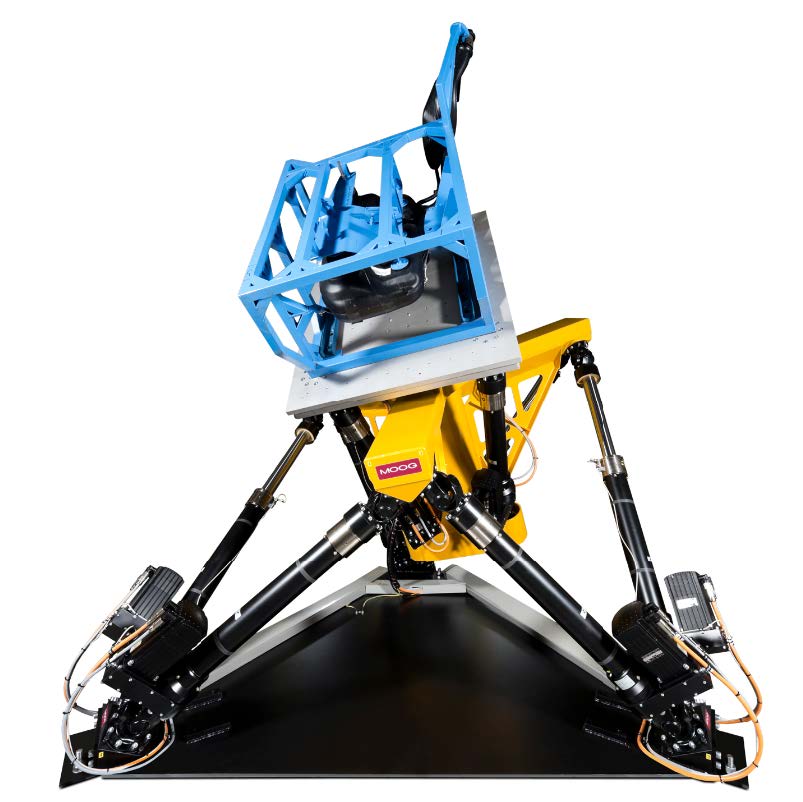
Fig. 4. 8 DOF Moog test system comprised of a 6 DOF Electric Simulation Table
with an innovative extra 2 DOF tilt table.
With an 8 DOF system, Fiat can now achieve total pitch and roll angles of more than 50 degrees and continual acceleration of up to 12 m/sec². Achieving a greater degree of combined pitch and roll angles with a simulator allows automakers like Fiat to avoid taking their prototypes to a test track. Being able to simulate the sharper cornering and higher acceleration found in real-life driving increases the speed of testing and saves cost, because it reduces the use of outdoor test tracks.
A Second Lap for the 8 DOF
When Veritas AG, a producer of fluid systems, molding parts and thermo systems for the automotive industry, wanted to test the behavior of fluid in automotive fuel and fluid tank systems, it selected Moog to supply an electric simulation table with tilt. Veritas AG ordered the 8 DOF system to perform tests on automotive SCR (Selective Catalytic Reduction) fluid tanks used to inject liquid-reducing agents in catalytic converters for the reduction of harmful emissions. Like Fiat, Veritas AG’s 8 DOF system consists of an electric simulation table with a tilt table on top for increased pitch and roll motion.
The electric simulation table reproduces the higher frequency road profiles, where the tilt table can simulate the cornering and acceleration behavior of the vehicle. This enables Veritas AG to include various conditions during driving that lead to extreme fluid-sloshing effects, such as instant braking or very sharp cornering maneuvers (See Fig. 5). In addition, the Moog Replication test software module will enable Veritas AG to replicate time history drive files that were recorded at the test track. After Moog installed the system, Veritas immediately began performing its first series of tests for its automotive customers and continues to see a steady line-up of work for the realistic testing the table provides.
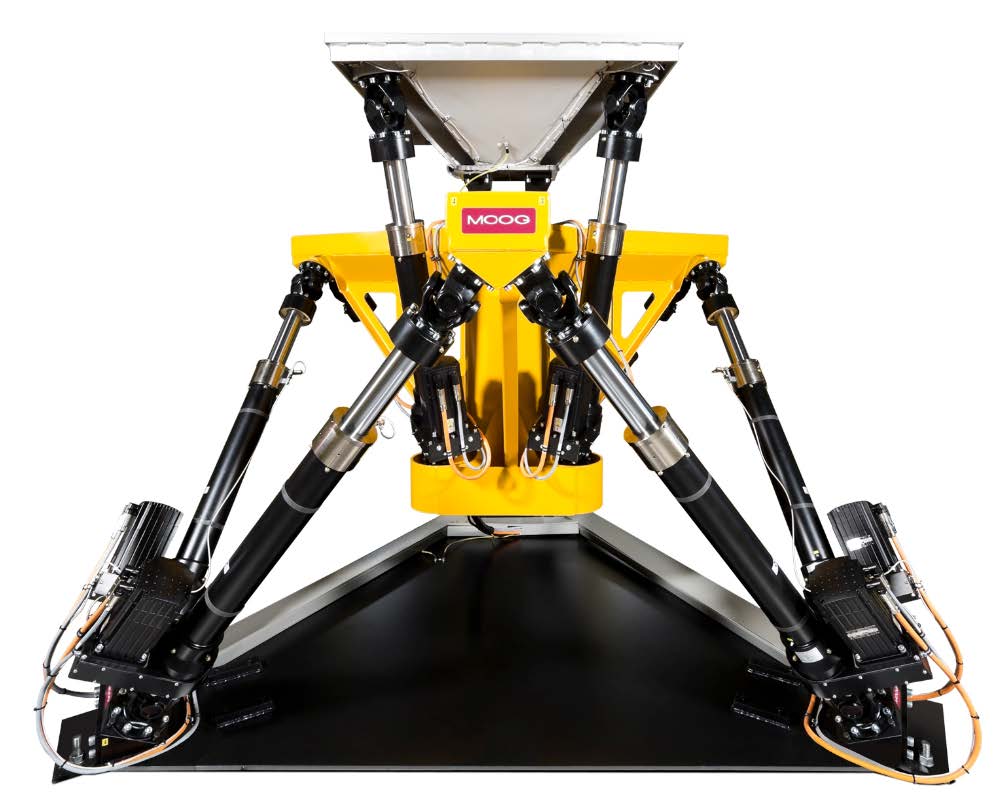
Fig. 5. The Electric Simulation Table with Tilt is used for
product development testing, such as fluid tank tests.
Bringing a Product to Market Faster, with Less Space
High frequency multi-axis vibration testing with electric or hydraulic simulation tables enables companies like Fiat, Veritas AG, CTI and XinDeBao to shorten the time needed for product testing and quality assurance through its highly realistic feel and ability to simulate a period equivalent to hundreds of thousands of road miles.
The simulation tables installed for companies like XinDeBao occupy only one-third of the space of traditional shaker tables. The smaller size makes it easy to install, move and control in any place in the testing laboratory. This gives automotive suppliers additional space for personnel and other equipment in their respective facilities. The tables are also less costly to maintain than orthogonal designs because the six actuators in each table are alike, so spare parts for any one table cost less.
For Fiat, Veritas AG, CTI, XinDeBao and other global customers, working with Moog means prompt local support that delivers turnkey solutions, and exceptional performance. Additionally, Moog offers a wide array of simulation products and can design the most appropriate configuration depending on a customer's test requirements and test article (i.e., components, sub-assemblies and systems). Ultimately, it’s a relationship that moves safe, profitable designs off the drawing table and onto the road faster.
Author
Will Opie is the head of Moog’s global simulation and test business. He has been with Moog for ten years in business development and program management roles in the defense, medical, automotive and aerospace markets. He studied mechanical engineering at the University of Plymouth in the United Kingdom.